Shipper | Case study
U.S. distributor mitigates disruption with up-to-date network model
Supply chain modeling provides 55% cost avoidance for hydroponics distributor.
From governmental regulations, port strikes, extreme weather events and more, network optimization models can provide the support to ensure agility (and possibly cost avoidance) when you need it most. Optimization models serve both strategic and tactical purposes for business planning situations across various supply chains. To strengthen your supply chain’s resistance to unforeseen events and prepare for unplanned opportunities, consider building and maintaining a model to help your business manage through disruptive events that happen all too often.
The situation
Before COVID-19 hit the United States, the largest distributor of hydroponic equipment in the U.S. commissioned Schneider to conduct a strategic supply chain analysis to recommend the best warehouse footprint to support their growth. These types of strategic engineering studies are multi-phase. As an early part of their normal progression, a network optimization model was created and baseline scenarios were run. The map below shows the distributor’s baseline customer assignments as bursts for each of their six existing warehouse regions
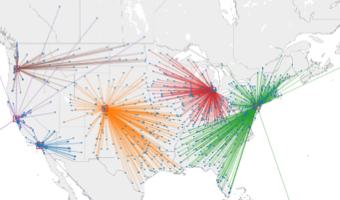
Original customer assignment
When COVID-19 reached the U.S. and started spreading, an employee at the hydroponic equipment distributor’s mountain-region facility contracted the virus. Per guidelines issued by The Centers for Disease Control (CDC) the facility needed to be shut down immediately for at least two weeks. This shutdown had the potential to create huge service issues for the distributor. Because quality service is an important element of the distributor’s business model, priority was placed on ensuring product could still ship. A solution was needed quickly, and the existing network optimization model and baseline scenarios made a more detailed analysis possible, which would prove valuable in the near future.
Speeding toward the solution: keep freight moving while minimizing cost exposure
With the information available from the baseline network model, Schneider’s engineering team got to work without missing a beat. The distributor requested the logical solution of Schneider–to reassign each end customer to a new warehouse based on distance.
Schneider delivered this “next closest” solution within one hour of being notified of their request. But the logical solution wasn’t ideal; while less than 8% of the volume had a negative service impact, (measured when a customer moved from one to two days of transit time) the additional cost of the solution was significant. And because the distributor was experiencing significant growth, capacity was an issue that these new assignments would further magnify, leading to service and delivery issues. Schneider’s engineering team delivered the original request but knew capacity needed to be considered in the solution to best serve the distributor and its customers, so they kept working.
Fortunately, network optimization models excel at considering more than one factor in a decision: how do we blend a solution that considers the “next closest” location with the need for reliable capacity and what is it going to cost? Because the data was current, within three hours the Schneider team was able to model and deliver a second scenario that took capacity and distance into consideration. The new optimal solution included not only facility capacity constraints but also inbound, outbound, transfer and handling costs. This solution reduced the outbound cost increase by 55% while also removing capacity issues. There would be no additional increase to transit time which meant service would be acceptable by the distributor’s customers.
Schneider then used the model outputs to predict volume by facility which allowed for better staff and labor planning for the open warehouses. To top it off, Schneider found additional carrier capacity to cover the new shipping lanes, ensuring everything shipped on time to operationalize the results from the network optimization model.
The value of network modeling
Pictures are worth a thousand words–let’s look at these side by side.
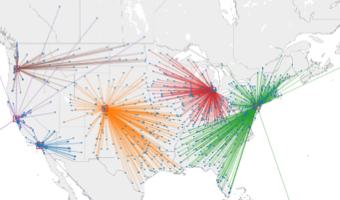
Baseline: The yellow burst representing mountain facility is visible. It is missing in the second two maps because the facility shut down.
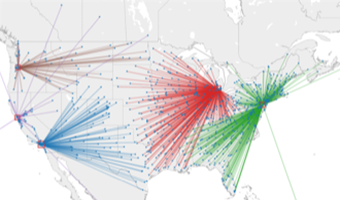
Next closest model: Logical, but left lots of gaps and was expensive.
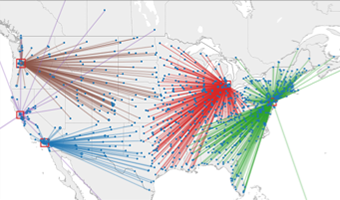
Optimized Supply Chain Model: This solution mitigates costs while honoring capacity and product constraints of each remaining facility.
Results
Cost Avoidance
Reduced 55% through network modeling (covering nearly half the distributor’s investment in the initial engineering work)
Distributor
Shifted workflows swiftly as a result of the up-to-date network model
Tactical mitigation solution
Delivered in less than three hours from initial request
New throughput calculation
Enabled better resource planning for each warehouse
Wider carrier base
Leveraged to cover expanded territories
Schneider's experienced supply chain operators
Provided guidance during crisis management
Close
By proactively working with Schneider’s supply chain engineers, the distributor set itself up for success – weathering disruptions in its supply chain, avoiding costs and seeing a near-immediate ROI in its initial investments.
These models not only serve both strategic and tactical purposes but, time after time, have been proven to manage events that disrupt supply chains, helping shippers of all sizes avoid costs and realize an ROI in their supply chain engineering investments
Drive your business forward
Sign up to receive our industry leading newsletter with case studies and insights you can put to use for your business.