Shipper | Case study 4 min. read
Delivering increased productivity and reliability to the forestry industry
Rocky Comfort Forest Products had a big problem - they couldn't get their logs hauled. Schneider came to the rescue with a consistent and reliable solution that changed their business.
An industry in need of a change
Schneider has a rich history of hauling countless materials, but the idea of moving freshly cut timber straight out of the woodland was new to the company.
So, what brought Schneider and forestry together? As with any successful customer story — a need and a solution.
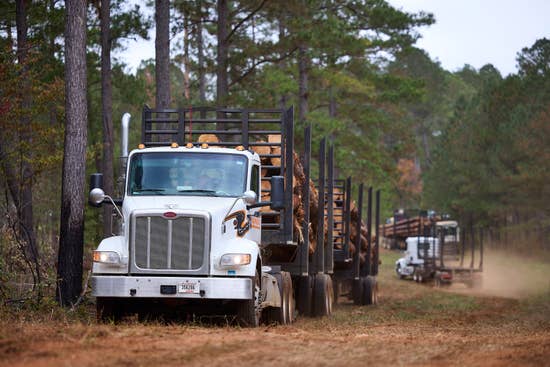
Getting timber to the mills had always presented challenges, but the COVID-19 pandemic made many industries — forestry included — acutely aware of imperfections within their transportation models. During the pandemic, the demand for lumber was wide open as people used their extra free time to remodel or build, and the harvested wood couldn’t flow to the mills fast enough.
Loggers were not able to focus on their competency
The specialized nature and remote location of logging results in owner-operators transporting most of the freight. Finding reliable and consistent capacity was difficult in that market for loggers, who are the ones typically tasked to make transportation arrangements. During times like the pandemic, it can be increasingly difficult to secure capacity, as truck drivers could have options to move more lucrative freight, at the ports or elsewhere. This setup at times can create a situation where the logger is not sure if they will have the trucks they need to move the round wood, which ultimately could halt the entire operation — and their paycheck.
Schneider’s optimized plan allowed the logger to focus on its core competency
It was around this time that Rocky Comfort Forest Products and Interfor came to Schneider for their expertise to optimize their transportation model.
The first thing the Schneider team did was dig in to understand the logger and forest products company, their goals, current processes and issues. With that data, the Schneider team analyzed the situation and brought its 90 years of transportation experience and expertise to the table to configure a custom solution for the logger and forestry products company working together.
The plan provided both Rocky Comfort Forest Products and Interfor with an approach that detailed the equipment, driver and process needs to provide consistent capacity and increase both productivity and tonnage (loads). The logger loved the plan, as it helped them focus on their core competency and what they do best — logging. The forestry products company loved it because it kept the flow of timber consistently coming into the mill.

Once all parties were aligned with the new transportation solution, Schneider got started with its first crew. As the crew ramped up its operations, Schneider worked with Rocky and Interfor to determine the right delivery pace and set driver expectations. Through these integral conversations and load executions, Schneider and the logger built a strong foundation of trust.
The drivers quickly got into a routine, executing a set-out system. They took their pre-loaded trailers from the tract, unloaded them at the mill, then returned to the tract to drop off each empty trailer and pick up another pre-loaded trailer. After proven consistency and efficiency, more drivers were added to keep up with the faster-paced process and keep the supply chain moving. Six months after assuming the transportation responsibilities for Rocky and Interfor, a second crew was added under the forest companies’ stumpage program.

Predictability and reliability drive positive results
Schneider and its dedicated forestry team of experts have become a provider that not only could handle, but optimized for, the complexities of transportation in the forestry industry. With this new solution, Schneider relieved the logger of the burden of transportation and allowed them to focus on, and scale, their core competency and do what they do best.
Since beginning to work with Schneider, the Rocky Comfort Forest Products and Interfor have:
- Developed a dedicated transportation solution, providing consistent capacity and safe, reliable, professional drivers.
- Increased tonnage output by 20%.
- Experienced reliability in scheduling freight deliveries to the mill.
- Gained a relationship with a transportation provider that goes beyond the requested solution and optimizes their operations.
The lumber market may not be running at the same frenetic pace as it was during the pandemic, but Schneider is continuing its work with numerous forestry operations to improve their transportation models, bringing predictability and reliability to their supply chains, no matter the market conditions.
Contact us
Learn how Schneider’s Dedicated service offering can help you achieve reliability and predictability in your forestry operations.
Drive your business forward
Sign up to receive our industry leading newsletter with case studies and insights you can put to use for your business.