Shipper | Case study
Integrating a new acquisition and reducing supply chain costs by more than $1 million
Background
A large manufacturer and distributor of specialized polymer materials and services was poised for business expansion and devised an acquisition strategy to deliver growth. When the manufacturer announced the acquisition of a leading producer of custom plastic sheet, roll-stock and packaging solutions, it was committed to a successful integration of the new acquisition. The manufacturer set a goal to deliver cost savings of $65 million by capitalizing on the synergies of the two companies. Driving supply chain and logistics efficiencies, along with better control, needed to be part of that cost-savings plan.
Situation
With customers becoming distraught and parts piling up on the dock, the manufacturer knew it had to act quickly and boldly. Timely delivery of its new acquisitions products is crucial to the successful operations of its customers. It knew that every day of missed deliveries only exacerbated the problem and would ultimately damage customer relationships as well as the brand.
That’s when the company turned to Schneider's Supply Chain Management (SCM) team. Based on previous business relationships, the manufacturer trusted Schneider’s capabilities and responsiveness. It relied on Schneider to deliver on promises and develop a freight management system to facilitate seamless integration with the new acquisition.

Solution
Working collaboratively, Schneider devised a strategy that integrated operations into a centralized command and control environment enabling consistent and reliable information, setting the stage for Lean Six Sigma projects and ongoing improvements. This harmonized supply chain strategy took advantage of the best of both organizations.
To implement this multi-faceted approach, the Schneider team needed to learn both companies’ logistics strategies and processes quickly to understand what would fit in or enhance the existing supply chain and what needed to be re-engineered. That was accomplished in the following manner:
- Designed a process and integrated data to ensure timely access to accurate information
- Developed and implemented a harmonized process and controls
- Identified and led logistics cost saving initiatives across a unified supply chain
The Schneider team established consistent metrics to manage all transportation elements, creating a system in which informed, data-driven decisions could be made
Results
Schneider’s expertise and experience made all the difference and the manufacturer is now positioned for future growth, saving more than $1 million in costs. The company is now able to focus on its core business and maintain its brand reputation while Schneider handles the transportation needs from start to finish. Many breakthrough results have been realized:
- Achieved 98 percent on-time delivery service
- Created an optimized network that made the most of supply-chain synergies
- Delivered operational visibility and network control
- Provided the business intelligence required for continuous improvement
- Generated sustainable savings in excess of $1 million annually
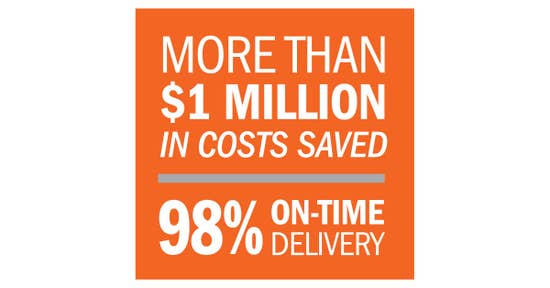
The program has been widely recognized across the manufacturers organization, earning Schneider the Supplier of the Year Award. And, the relationship between Schneider and the manufacturer continues to grow.
Drive your business forward
Sign up to receive our industry leading newsletter with case studies and insights you can put to use for your business.