Shipper | Case study
Manufacturer gains consistent cross-border intermodal capacity
Manufacturer requires in-demand product to flow through the pipeline
A leading North American plumbing and building products manufacturer produces multiple brands of high performing bath and kitchen fixtures. The product needs to be transported from its facilities and distribution centers located throughout Mexico to an extensive network of wholesalers and specialty big-box retailers in the U.S.
Volatile markets drain outbound efficiencies
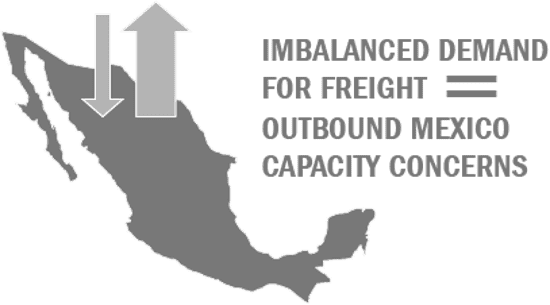
Today, the outbound demand is significantly higher than inbound Mexico demand. This imbalance decreases the reliability of capacity traveling from Mexico to the U.S. Appreciation of the U.S. dollar due to the U.S. economy’s recovery negatively affected the exchange rate for the peso, expanding the gap between imports and exports. Even when the Mexican peso is supported by a strong national economy, volatility in the markets has led companies to purchase less merchandise from the U.S. and develop local suppliers to reduce import costs. The manufacturer, like many others, struggled to obtain the capacity it needed across the border and needed a reliable, consistent solution to ship final product to it’s distribution channel in the U.S.
Cross-border service secures northbound shipment of goods
Schneider has more than 25+ years of experience in Mexico, providing the expertise and know-how to successfully manage cross-border freight. Schneider began its relationship with this manufacturer in 2012 by providing northbound intermodal service. Shippers who use Schneider’s cross-border intermodal door-to-door transit – which delivers truck-like service with competitive pricing and delivery times – experience decreased risk of delays and increased security. Schneider quickly became the primary intermodal provider thanks to increased supply chain efficiencies and reduced spending on non-value-added services, such as border transfers and transloading.
In 2013, Schneider proposed a more secure cooperative plan to offer strategic intermodal pricing and cross-border capacity planning and service. The agreement included implementation of service, joint planning and ongoing analysis:
Joint Planning
- Schneider Intermodal provides service to the U.S. and Mexico, ensuring enough containers are in Mexico to provide much-needed inbound U.S. capacity.
- Schneider’s bilingual operations in Mexico are strategically placed to be easily accessible for the customer’s daily needs.
- Schneider’s operations team in Mexico is in contact with the Mexican carriers from the manufacturer’s facilities to the intermodal ramp.
- The manufacturer provides a weekly forecast, allowing Schneider to provide container availability confirmations within the next 24 hours – which results in better capacity planning and proper container placement.
- Schneider communicates with Mexico Operations and the customer service team twice daily to forecast loads moving to the two intermodal ramps.
Implementation of Service
- Schneider provides local drayage in Mexico from the manufacturer’s three distribution centers to the rail ramps through the use of a dedicated fleet of Customs-Trade Partnership Against Terrorism (C-TPAT)–certified Mexican carriers.
- Schneider’s carrier base in Mexico is 100 percent C-TPAT certified, enabling high security levels along the transportation chain.
- Schneider’s simplified load configuration process with stackable, 53-foot orange intermodal containers provides reliable, door-to-door, truck-like service.
Ongoing Analysis
- Schneider implemented a geofencing tracking system to monitor freight location and provide real-time delivery information, which helps prevent cargo theft on each load.
- Schneider audits contracted carriers every six months with facility visits on C-TPAT criteria.
- Security specialists monitor C-TPAT data daily and meet every two months to review.
Reliable safeguarded service and a flourishing relationship
Schneider Intermodal continues to meet the manufacturer’s service requirements, exceeding customer pickup and delivery expectations. Special certifications, open communication and meaningful technology provide concrete time and cost efficiencies, superior security practices and reliable, consistent capacity for the manufacturer.