Shipper | Case study
Manufacturer reduces costs nearly 35% by centralizing supply chain management processes
Background: large automated components manufacturer needs better control of its supply chain
A large automated components manufacturer and distributor had ten unique strategic business units with supply chains each operating independently, utilizing ineffective and aging technology. Faced with rising costs, poor business processes and deteriorating service, the company turned to Schneider to assist with a company-wide supply chain transformation.
Situation: leveraging a lead logistics provider network to improve performance and reduce cost
In this industry, time to market is critical. The competition between component suppliers is fierce and a stronger, faster, highly reliable supply chain is a competitive advantage. The original equipment manufacturers (OEM) that rely on these components have strict production schedules and need to serve their own customers. This creates pressure on suppliers to meet delivery schedules. Most OEMs don’t keep a large parts inventory, opting for just-in-time manufacturing practices which mean a late delivery could result in a costly line shut down.
In addition, the competitive landscape demands a tight control on costs. With fluctuating prices of raw materials and other elements of the business, better management of supply chain costs are vitally important to managing bottom-line performance.
The right solution would have to be efficient and deliver the visibility and flexibility that could work across all of the company’s strategic business units. It needed a best-in-class technology platform and a centralized management strategy to leverage the existing network synergies for cost reduction and improve performance within the supply chain.
Schneider's solution: optimize freight moves to maximize efficiency and reduce waste
To gain control of the overall supply chain and ensure efficient execution, Schneider needed to revamp the manufacturer’s business processes, implement a new technology platform to drive efficiencies into multiple processes across the supply chain and reduce overall costs. Schneider brought a number of solutions to the table:
- Risk Management: Standardized all carrier contracts to meet the customer's requirements while monitoring insurance certification expirations, DOT safety ratings and CSA scores.
- Freight Payment Authorization: Before Schneider engaged, if an invoice was presented it was paid without validation or audit. Schneider implemented a Freight Authorization File and process to ensure the appropriate amount is paid to each carrier.
- New EDI Interface created faster order processing and cycle times, plus the integration enabled nearly real-time visibility and enhanced the planning process.
- Regional LTL Shipping (“Zone Skipping”) reduced transportation expense and improved quality by eliminating multiple terminal and product handling while enabling faster and safer transit of the products.
- Major labor related disruptions at the port were avoided because Schneider was able to help create a solution that diverted freight and quickly developed new product flows.
Results: Schneider's tailored solutions exceeded expectations
By working with Schneider, the customer was able to reduce costs by nearly 35 percent – well beyond its expectations. At least 10 percent of that reduction came from leveraging TMS technology optimization, revamping business processes for increased planning visibility and by using Schneider transportation procurement services to establish reliable, market-sustainable rates.
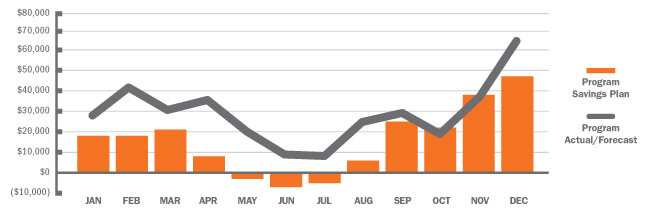
In addition, the customer gained comprehensive life cycle visibility to each order, creating faster transit through converting freight away from LTL and leveraging network density and volume more efficiently. The technology deployed allowed for speedy route assignments and optimization, even as the network shifted to meet changing business needs.
The results have been exceptional. This manufacturer has benefited through sustainable ROI and increased service levels to its customers which have resulted in year-over-year business growth at a higher margin due-in-part to the significant reduction in transportation costs.
To understand how our supply chain management experts can uncover savings in your business,
email solutions@schneider.com
Drive your business forward
Sign up to receive our industry leading newsletter with case studies and insights you can put to use for your business.