What to look for when choosing an intermodal carrier
Intermodal transportation has seen a surge in popularity due in large part to increased consumer demand and the ballooning cost of moving product over the road. Shippers are turning to this mode now more than ever, and with good reason: It’s cost-effective (and most beneficial) when freight moves 300 miles or more, goes to the same metro location consistently, and shippers are within 250 miles from a ramp.
To get the most out of intermodal shipping and mitigate the headaches of managing your supply chain, it’s crucial to choose a carrier that can guarantee capacity and find efficiencies. Consider these six intermodal carrier traits for strategic and cost-efficient intermodal shipping.
1. Holds long-term, strategic relationships with rail providers
When a transportation and rail provider routinely and productively collaborate, they develop a strategic working relationship. But that magic doesn’t happen overnight. It’s the result of the transportation provider committing to consistent, regular volume of freight throughput. And when the transportation provider’s network complements the rail provider’s, the overlapping footprint makes for easier and more efficient freight moves. Over time the two form a mutually beneficial relationship, which helps a carrier with securing capacity and getting freight moved with less risk of getting bumped to the next departure.
For this relationship to form, the rail needs to know it can rely on a carrier to provide a specific amount of volume regularly. The carrier is then given that capacity before other third-party providers even get to request what they need. The carrier gets priority until that capacity threshold is reached, and if the carrier needs more, it has the credibility to request additional placement based on past freight volume reliability. During changing market conditions or an unexpected surge, an established carrier can flex its capacity needs within a larger window of time. The rail will work to prioritize and accommodate the request before turning to less-established carriers looking to change their capacity needs.
An intermodal carrier without an established relationship is typically unable to secure timely placement on the train, let alone enough capacity. This setback can result in several days tacked on to the shipping duration. Providers with priority placement can expect a 2-4 day delivery window, whereas a carrier without rail relationships could see freight take anywhere from 5-7 days to be delivered.
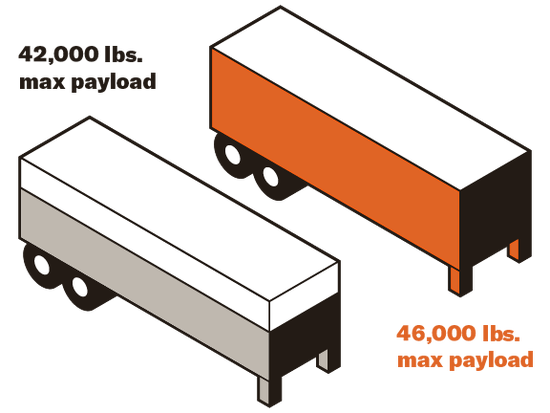
2. Continuously invests in shipping equipment for guaranteed capacity and visibility
When demand for capacity increases, so does demand for equipment. And when every pound and inch matters, the right equipment becomes even more essential to maximize intermodal capacity. Unfortunately for shippers and intermodal carriers alike, rail companies focus more on optimizing their networks than they do supporting them with intermodal shipping equipment.
Chassis
It’s important to leverage an intermodal carrier that owns and maintains its own inventory of intermodal shipping chassis. Shippers should avoid working with intermodal carriers that rely on a shared chassis pool, as there is uncertainty in equipment availability, consistency and reliability.
- Availability: In the shared pool, the demand is often greater than the supply. If there aren’t enough chassis available at the ramp, product will sit, causing costly delays.
- Consistency: Chassis have varying weights — up to a 700-pound difference between models. To avoid fines, shippers have to assume that they’ll get a heavy chassis, which limits the payload. Schneider has a standard chassis that is 700 pounds lighter than the lightest chassis in the shared pool. This allows customers to move up to 46,000 pounds of product — up to a 10% increase in payload .
- Reliability: The shared pool doesn’t guarantee peak operating condition of its chassis, making breakdowns a common occurrence. A provider with owned assets, like Schneider, is more vigilant with monitoring the maintenance of its chassis fleet. Issues are identified and repairs made before they become too costly to fix — or need to be replaced altogether. For Schneider, specifically, it has a maintenance presence at almost all of its rail lamps, maintaining a 97% availability on chassis. Additionally, Schneider has approximately 100 service trucks that visit rail facilities and customer locations. This allows Schneider to have first priority of repairs, instead of having to call a vendor for repairs.
Uncertainty around chassis use may lead to unnecessary fees, delays and accidents.
Shipping containers
Strategic shippers using intermodal should prioritize providers that heavily invest in their own shipping containers. It’s a sign of assured freight capacity, as well as increased care in ensuring no goods are damaged along the way.
The size of freight containers can greatly impact the cubic capacity of the load and overall transportation costs. Cubing out is common, but pinwheeling pallets can increase the capacity of the load. A pinwheeled configuration is when the direction of every other pallet is altered. A common interior container width is 98 inches, which leads to cubing out sooner. However, transportation providers with containers that have more than 100 inches of interior width more easily allow pinwheeling. This increases the amount of freight moved per load and decreases transportation costs due to fewer overall loads moved. Schneider’s intermodal containers are 53 feet long with an interior width of 100.375 inches — easily accommodating the needs of shippers looking to maximize their loads.
24-7 tracking
Another critical piece of equipment for safely and efficiently moving freight is the use of satellite tracking for door-to-door visibility. As the supply chain becomes more complicated, the importance of real-time visibility cannot be overstated. These days, it’s becoming less of a nice-to-have and more of a must-have.
Complete freight visibility for intermodal moves is harder to achieve, making it a true differentiator when a transportation provider can deliver that clear line of sight into freight’s status. The key benefits for shippers include real-time, pertinent details regarding delivery status, delays and pending penalties. An intermodal transportation provider should be embracing GPS tracking technology to achieve complete asset visibility for improved security and mitigated risk of lost equipment. In connection with an API, automatic order updates can be sent, eliminating status concerns and the need for freight status requests.
Schneider FreightPower®, an online marketplace for instant access to capacity, is available for intermodal loads, allowing shippers to independently quote, book and track a load. This provides complete freight management and visibility with 24-7 tracking and notifications.
Having real-time analytics available helps shippers optimize intermodal operations, further enhancing their supply chains.
3. Manages dray transportation with its own team of professional, safe drivers
The driver shortage has been a top trucking industry issue for many years, and it’s showing no signs of stopping. In fact, American Trucking Associations estimates that the industry shortage is expected to surpass 160,000 drivers by 20301. High demand, fewer new drivers entering the industry and Baby Boomer driver retirements are all contributing factors. While no transportation provider is left untouched by the shortage, companies that employ drivers versus moving freight strictly through third-party capacity are more vulnerable.
Brokers may not be able to secure a driver when a shipper needs a load moved since they don’t have their own driver associates at the ready. Transportation providers with their own drivers are better able to meet shippers’ on-demand needs — even in a tight market.
Safety is also a crucial component to moving freight. Without question, drivers need to be trained to safely handle their truck, in- and out-of-cab technology and the freight itself. Shippers should look for transportation companies that go above the federal law in screening and training their drivers. One example is requiring urinalysis and hair follicle testing to remove unqualified candidates. Companies that invest in hair testing and monitor and treat sleep apnea in their drivers indicate advanced safety measures, so shippers can be assured freight is moved safely, securely and legally.
4. Has a dedicated load engineer for unmatched optimization and safety
To further help optimize loads, ask whether the transportation provider has a load engineer on staff. A load engineer oversees and supervises outbound freight, analyzing loads and determining the most efficient and safe ways for them to move. They have advanced knowledge of how to best optimize a container to maximize payload while also keeping safety in mind. In some instances, they will design and build special structures to ensure maximum payload and safety.
After analyzing the freight and determining the best way to maximize the space of the container, a load engineer must also consider the physical forces that affect a load during transit. Vibration and shock are the two main ones that affect freight during rail transportation, both of which occur continuously throughout the journey. Failure to control these forces can jeopardize the safe, damage-free movement of the freight. The load engineer will apply the best blocking and bracing measures based on the configuration to mitigate freight damage, and by extension, costly claims. Depending on the type of freight and how it’s loaded, multiple methods may be used to keep freight in place for maximum security.
5. Overcomes PSR-related freight disruptions
As rail networks shift to a new transportation model called Precision Scheduled Railroading (PSR), shippers can expect ramp closures, poor service from upended networks and increased costs from loads converting to competitive networks.
To avoid the inefficiencies and costs of transitioning to PSR, shippers have two viable options:
- If possible, shippers should diversify their rail network to ship with intermodal providers, like Schneider, using CSX and UP, which are rail networks that have already implemented PSR and now offer increased train velocity and decreased terminal dwell time.
- If a shipper’s network can’t align with the CSX and/or UP rail, then the next best option is to work with a multimodal service provider that can help determine the proper mix of transportation modes based off the business’s unique freight characteristics.
6. Facilitates a thorough onboarding process to mitigate freight mismanagement
No shipper wants to regret the decision to switch providers. A key factor in a successful transition is selecting an intermodal carrier that offers a step-by-step onboarding process with specially trained intermodal new business team members. To ensure business is set up for long-term success, shippers should be asking their potential providers:
- How do you plan to align our network?
- Is there a single channel of communication?
- Are there regular check-ins?
- What resources do you offer to help become a shipper of choice?
The most important action strategic shippers can take is to ensure they’re using an established, strategic intermodal shipping provider. In doing so, they’ll obtain flexible, consistent capacity and know that they have a smart provider working on their behalf to find efficiencies and move freight safely.
Contact us
For more information on what to look for when evaluating an intermodal carrier, contact us.