Shipper | Best practices
6 tips on how to safely ship temperature-sensitive freight
Managing extreme temperatures now top of mind for shippers.
How to keep temperature-controlled freight fresh
With severe weather events becoming more frequent, shippers are facing increasing challenges with keeping food and beverage products safe during extreme temperature swings.
Shippers need to control and plan for what they can more than ever before to keep product on shelves and reduce claims. Here are six tips on how to safely move temperature-sensitive freight in hot or cold weather.
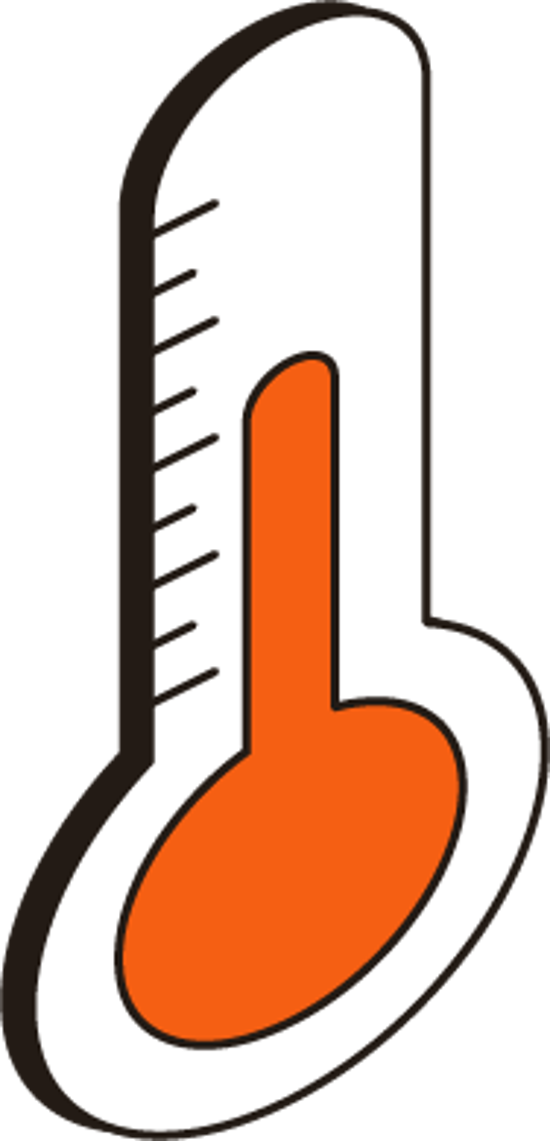
1. Get food and beverage freight away from the trailer wall
Food and beverage products loaded against a trailer or shipping container wall will be the same temperature as outside the trailer within 24 hours. Conduction (the transfer of heat or cold from one object to another) can wreak havoc on temperature-controlled freight. For an unscientific test, place your hand on the outside of a container and then on the inside wall. Unless the trailer is facing direct sunlight, the temperature will be the same. Now slowly move your hand away from the wall. You will notice that as soon as your hand moves away from the wall the temperature changes and will continue to change until you are about four inches from the wall. Center loading of freight away from the walls is strongly recommended to eliminate the impact of temperature — and the farther away from the walls, the less the chance of conduction.
- 1" = 15% heat/cold transfer
- 2" = 10% heat/cold transfer
- 4" = 5% heat/cold transfer
Product is loaded tight against the walls in intermodal to prevent load shifts. However, rail providers have approved the use of dunnage, or loose wood or matting that keeps cargo in place, to fill voids and maintain a distance of 4" between the sidewall and shippers’ products. A variety of options are on the market, from airbags to foil-backed fillers, styrofoam panels and folding fillers. Some shippers have also successfully used old pallets as dunnage. Carrier loading engineers can help you create a loading pattern that will protect food and beverage products from damage and temperature and keep product moving via the rails safely. Some shippers maintain two loading patterns, one for times or destinations that do not require temperature protection and one for when it is needed.
2. Get the product off the floor of the shipping container to prevent conduction
Conduction doesn’t just happen against the sidewall, it also comes through the floor. The solution is simple: Ensure that pallets are used to create a barrier between the product and floor.
3. Use blankets — over and under pallets — to slow transfer of heat or cold
Blankets are effective in slowing the transfer of heat or cold but need to cover the product completely. Research simulating temperature changes conducted by the EPA, Protek and Schneider at Texas A&M revealed that blankets or other insulation placed under freight, on the floor of the container, are just as critical as having insulation over and around the pallet. Doing so reduces the loss of heat/cold through floorboards. The research discovered that contrary to popular belief, heat/cold is not being transferred from the floor to the product when sitting directly on it. Instead, heat/cold is escaping the trailer via the floor and putting the product at risk.
Knowing this, retention and maintenance of optimal temperatures is a must and can extend the life of a shipment by two to three days. Loads tested side by side showed a 12-degree difference when floor product was used.
4. Raise or lower the temperature at loading
Blankets slow the transfer of heat, but timing is everything. Capturing heat in the winter and cold in summer means your product will be protected longer and have more time before exceeding your temperature threshold. If you’ve used an engine heater, you will understand this concept. Plugging in a block heater of a cold engine has no impact. Plugging in an engine heater as soon as a warm engine has been turned off maintains the temperature of the engine so that it will quickly start even in frigid temperatures. By starting at the desired temperature, you have made the blanket more effective (on top and bottom of the pallet) and given your food and beverage product more time before it will exceed its maximum threshold.
5. Monitor the weather between shipping origin and destination
Monitoring the weather is complicated: Not only do you need to monitor temperature and conditions at your points of origin and destination, you need to include all of the points in between. Doing so needs to be an additional task on your daily to-do list and can be done manually via the internet or by using a service which monitors the temperature throughout the planned transit.
6. Partner with the right food and beverage carrier
Finding the right food and beverage carrier is essential. Asset-based carriers that own their equipment, like Schneider, have resources to help you develop the right plan for your freight. Schneider’s experienced load engineers work directly with customers to develop a customized plan for your specific freight needs and run test loads to set you up for success. Read more about how Schneider can help your business navigate food and beverage logistics at our food and beverage shipping services page.
Find a food and beverage carrier
Learn how Schneider can help your business navigate the logistics of temperature-controlled freight in any weather.
Drive your business forward
Sign up to receive our industry leading newsletter with case studies and insights you can put to use for your business.